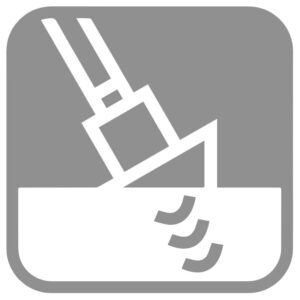
Il Controllo Non Distruttivo (CND) è il processo di ispezione, verifica e valutazione di materiali, componenti o assemblati per ricercare discontinuità o valutare caratteristiche, senza distruggere la parte. I CND sono utilizzati nella produzione, nella fabbricazione e in servizio, per garantire l’integrità e l’affidabilità del prodotto, per controllare i processi di produzione, ridurre i costi degli stessi e mantenere un livello di qualità uniforme. I CND vengono utilizzati per garantire la qualità dei materiali e dei processi di saldatura durante le fasi di fabbricazione e montaggio, vengono anche utilizzati per garantire che i prodotti continuino ad avere l’integrità richiesta durante il servizio. Poiché i Controlli Non Distruttivi non alterano in modo permanente l’oggetto da ispezionare, è una tecnica di grande valore che può far risparmiare tempo e denaro nella valutazione del prodotto, nella risoluzione dei problemi e nella ricerca.
Un comune ed efficiente metodo per valutare l’integrità di un componente, viene effettuata tramite ultrasuoni. Quando una forza esterna è applicata ad un materiale elastico, questo materiale è soggetto ad una deformazione e le sue particelle cominceranno a vibrare attorno alla posizione di equilibrio. Le vibrazioni vengono trasmesse alle particelle adiacenti e in questo modo la perturbazione si propaga nel materiale. Questa perturbazione rappresenta l’onda ultrasonore che viaggia nel materiale. Alla base della propagazione degli ultrasuoni vi è il principio di Huygens.
Quando gli Ultrasuoni incontrano un materiale di diverse proprietà acustiche, parte dell’energia viene riflessa e ritorna al trasduttore che può catturarla e misurarla. Ci sono diversi tipi di onde ultrasonore: longitudinali, trasversali, di superficie, di Lamb. Tutti i tipi di onde sono caratterizzati da diversi parametri quali: velocità di propagazione, frequenza, lunghezza d’onda, impedenza acustica, pressione, intensità. A titolo di esempio, le frequenze tipiche degli Ultrasuoni vanno da circa 20kHz a 20MHz.
Ultrasuoni Automatizzati (AUT)
Le origini del metodo risalgono al 1959, ma le prove pratiche sul campo non sono state effettuate fino al 1972. A quel tempo gli operatori iniziarono a studiare la fattibilità dell’utilizzo di tecniche di saldatura meccanizzate per sostituire il tradizionale processo manuale di saldatura ad arco metallico schermato. Durante la valutazione del processo di saldatura, è stato determinato che parti della saldatura venivano scarsamente ispezionate dalla radiografia tradizionale a raggi x. Infatti questa tecnica si basa sull’orientamento del difetto parallelo al raggio per consentire il rilevamento. Per affrontare questa lacuna è stato avviato un programma per sviluppare un sistema di ispezione ad ultrasuoni automatizzato.
Dall’applicazione iniziale nel 1993, la ricerca e lo sviluppo hanno continuato a utilizzare i principi di questo metodo.
Intorno al 1996, le sonde Phased array piezoelettriche standard sono state studiate per ridurre la massa della testa di ispezione e per estendere l’intervallo di spessore testato. Il primo sistema phased array è stato qualificato per l’uso su pipeline nel 1999. Da allora lo sviluppo è continuato sia per l’hardware che per la parte software.
Il sistema PipeWIZARD convenzionale, che utilizza più trasduttori in modalità pulse-echo o tandem, è stato modificato da R/D Tech per produrre una versione phased-array chiamata PipeWIZARD Phased Array. PipeWIZARD-PA è l’acronimo di: “Pipe Weld Inspection using Zone discrimination And Real-time Display with Phased Array”.
PipeWIZARD-PA è un sistema di ispezione ad ultrasuoni automatizzato per saldature circonferenziali, principalmente per tubazioni di gas e olio da 4 “fino a 60” di diametri e da pochi millimetri fino a 50mm e più di spessore della parete.
L’obiettivo dell’AUT è quello di essere in grado di agganciare l’unità di ispezione, ispezionare la saldatura, interpretare i dati, contrassegnare i difetti, rimuovere l’unità di ispezione, salvare i risultati su due supporti separati e passare alla saldatura successiva in pochi minuti (sia offshore che onshore).
I Phased Array, a differenza degli ultrasuoni convenzionali, generano e ricevono ultrasuoni elettronicamente. Una serie di elementi (detto “array”), ciascuno collegato a un pulsatore separato e a un generatore di ritardo temporale, viene pulsato utilizzando una legge focale. Questa legge focale definisce quali elementi devono essere pulsati e con quale ritardo temporale. Regolando i ritardi temporali, è possibile generare fasci normali, fasci angolati, fasci focalizzati o non focalizzati, onde di taglio o onde longitudinali, a seconda delle caratteristiche degli elementi, zoccoli, e altri parametri.
L’electronic scanning, che sia esso lineare, settoriale o DDF, è considerevolmente più veloce rispetto al metodo convenzionale. Ciò da un enorme vantaggio alla tecnica phased array in termini di velocità di scansione e affidabilità. Il fatto di poter orientare il fascio nell’ispezione di geometrie complesse, offre delle possibilità che gli ultrasuoni convenzionali non avevano. Gli array possono essere molto piccolo, il che è un vantaggio quando c’è a disposizione uno spazio limitato
La “zone discrimination” è una tecnica di ispezione utilizzata con il PipeWIZARD che divide la saldatura in una serie di zone ben definite, ciascuna ispezionata dal proprio trasduttore focalizzato o da leggi focali se si utilizzano sonde phased array.
La metodologia è conforme a DNVGL-ST-F101 e ASTM E1961.
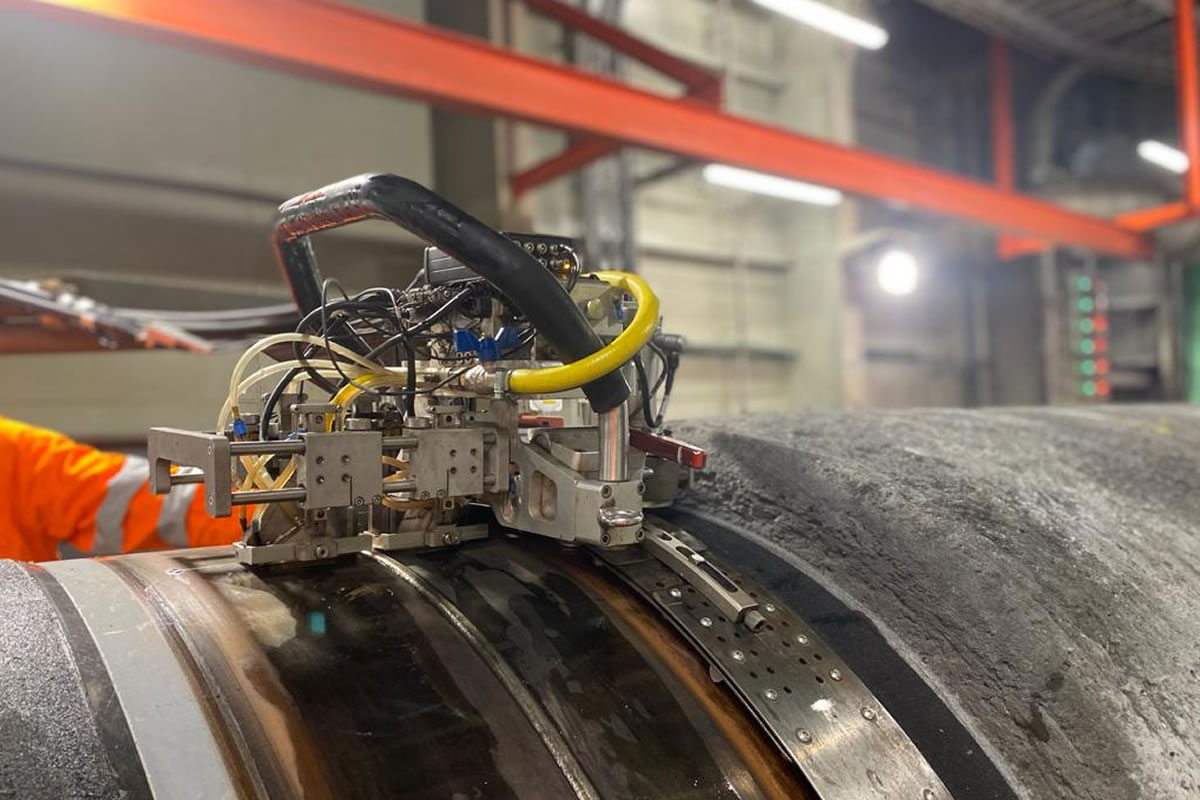
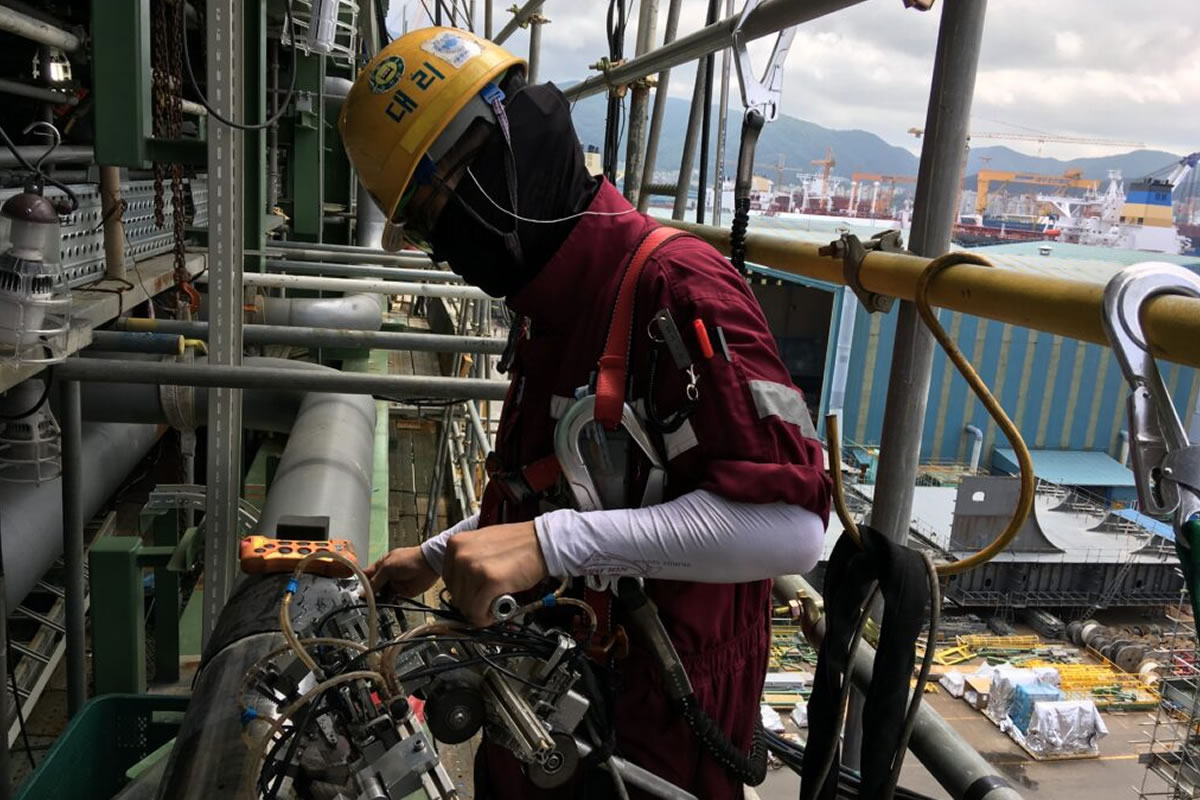
Controlli ad Ultrasuoni Phased Array (PAUT)
Le ispezioni phased array vengono eseguite utilizzando una sonda con più elementi che possono essere attivati individualmente. Applicando opportuni ritardi, il phased array è in grado di generare un fascio ultrasonoro, modellandolo in base alle caratteristiche desiderate di: apertura, angolo e messa a fuoco (formazione elettronica del fascio).La legge focale può anche essere modificata dinamicamente tra gli impulsi, consentendo così un movimento efficace del fascio di scansione (scansione elettronica).
Un fascio angolato si ottiene applicando un ritardo temporale di impulso costante ad elementi consecutivi dell’array (legge focale lineare).
Il focusing si ottiene regolando i ritardi temporali degli impulsi degli elementi al fine di ottenere una sequenza a forma di parabola, simmetrica rispetto all’array emittente (legge focale quadratica). Ciò consente al phased array di generare un fascio focalizzato a qualsiasi profondità (all’interno del campo prossimo).
I dati risultanti possono essere combinati per formare un’immagine visiva che rappresenta una sezione della parte da ispezionare. I dati acquisiti dal phased array durante la scansione possono essere visualizzati in tempo reale in tutti i formati utilizzati dagli strumenti digitali: A-scan, B-scan, C-scan e D-scan.
Time of Flight Diffraction (TOFD)
La tecnica TOFD (Time of Flight Diffraction) si basa sul fenomeno della diffrazione d’onda e misura il tempo di volo delle onde diffratte dalle estremità di una discontinuità. La tecnica TOFD utilizza due trasduttori situati sui lati opposti di una saldatura con i trasduttori impostati a una distanza specificata l’uno dall’altro. Un trasduttore trasmette onde sonore e l’altro trasduttore funge da ricevitore.
Ogni volta che un raggio d’onda incidente colpisce un difetto, la sua superficie genera un’onda riflessa, mentre le sue estremità agiscono come nuove sorgenti puntiformi di onde sferiche a bassa ampiezza che si propagano in tutte le direzioni (onde diffratte). Amplificando ed eseguendo questi segnali attraverso un computer, la dimensione e la posizione del difetto possono essere determinate con una precisione molto maggiore rispetto ai metodi UT convenzionali.
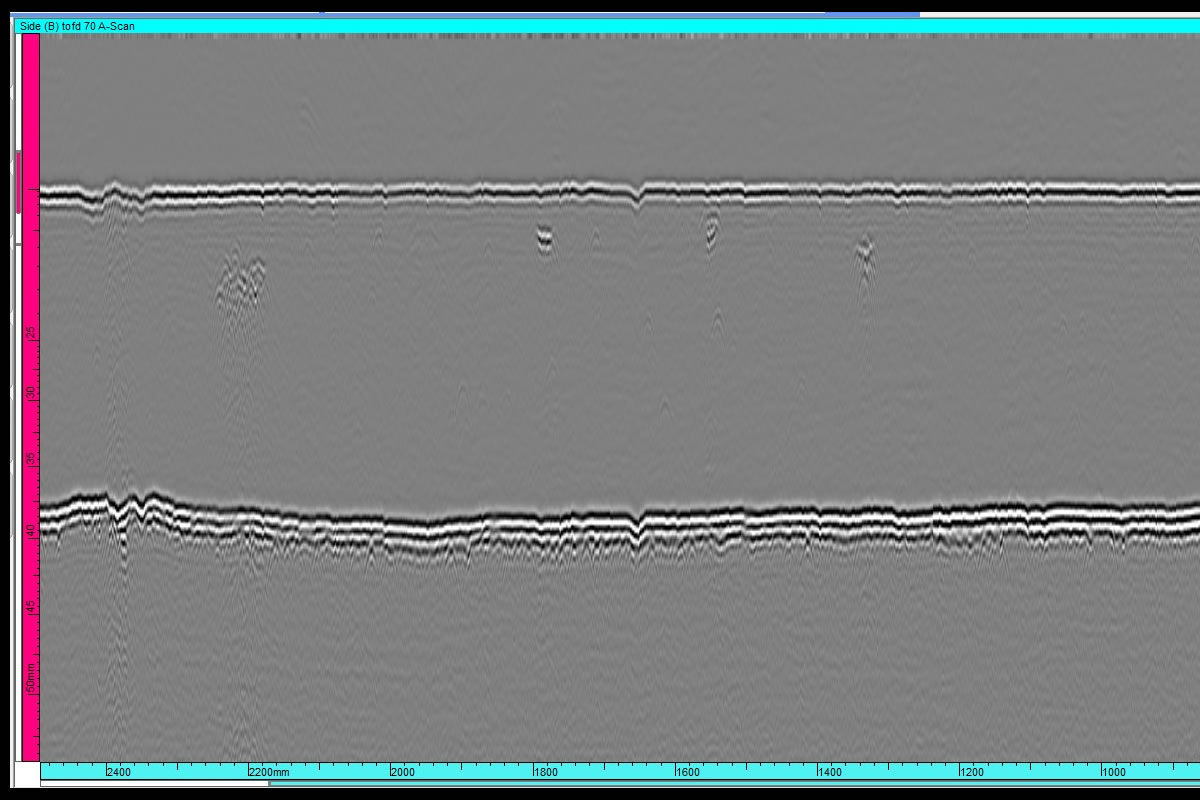
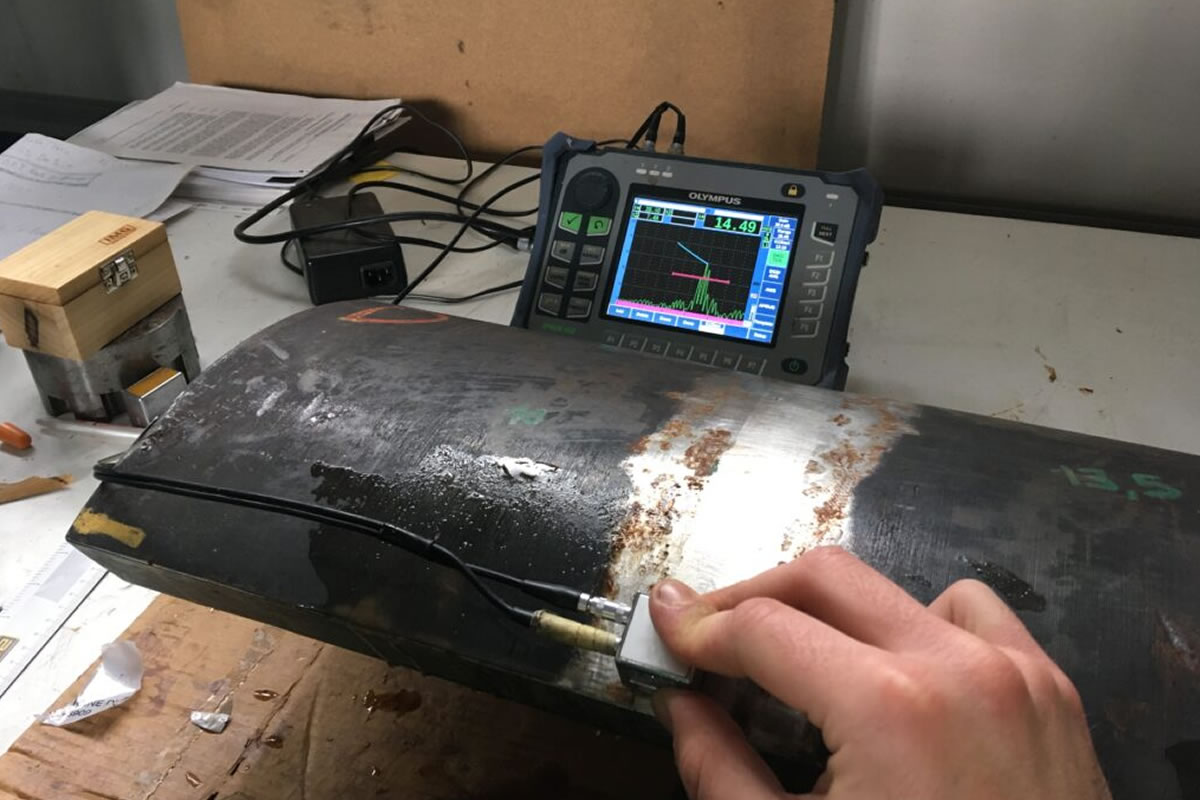
Controlli ad Ultrasuoni (UT)
Il suono ad alta frequenza viene introdotto nella parte da ispezionare e se colpisce un materiale con un’impedenza acustica diversa (densità del materiale e velocità acustica), parte dell’energia verrà riflessa e potrà essere mostrato su un display. Conoscendo la velocità del suono nel pezzo controllato ed il tempo necessario affinché il suono ritorni all’unità di invio (trasduttore), è possibile calcolare la distanza dal riflettore. Le frequenze sonore più comuni utilizzate negli UT sono comprese tra 1,0 e 10,0 MHz, in quanto sono troppo alte per essere ascoltate e non viaggiano attraverso l’aria. Le frequenze più basse hanno una maggiore potenza penetrante ma una minore sensibilità, cioè una minore capacità di rilevare piccole indicazioni, mentre le frequenze più alte non penetrano così profondamente ma possono rilevare indicazioni più piccole.
Il suono viene introdotto nella parte utilizzando un trasduttore ad ultrasuoni (“sonda”) che converte gli impulsi elettrici in onde meccaniche, quindi converte il suono di ritorno in impulsi elettrici. Questo segnale può essere visualizzato come rappresentazione visiva su uno schermo digitale o LCD. È possibile determinare la distanza dal trasduttore al riflettore. Il segnale può anche essere interpretato dagli operatori per determinare il tipo di discontinuità (mancanza di fusione, scorie, mancanza di penetrazione in radice, intagli, porosità, segregazioni). Poiché gli ultrasuoni non viaggiano attraverso l’aria, viene utilizzato un accoppiante tra la faccia del trasduttore e la superficie della parte da controllare per consentire al suono di propagarsi.
Sistema di ispezione rotativa interna (IRIS)
IRIS è una tecnica ad ultrasuoni applicata all’ispezione dello spessore residuo della parete dei tubi e fasci tubieri. È più accurato di altre ispezioni e restituisce informazioni sulla geometria del difetto e sullo spessore residuo della parete. Viene spesso utilizzata in combinazione con correnti indotte o metodo Remote Field Testing.
Controlli Elettromagnetici*
I test elettromagnetici sono una categoria di test che include test a correnti indotte, ACFM (Alternating Current Field Measurement) e RFT (Remote Field Testing). Tutte queste tecniche utilizzano l’induzione di una corrente elettrica o campo magnetico in un conduttore, e l’effetto risultante viene registrato e valutato.
Principio di base: quando una bobina viene stimolata con una corrente elettrica alternata, produce un campo magnetico intorno a sé. Questo campo magnetico oscilla alla stessa frequenza della corrente che attraversa la bobina. Se la bobina si avvicina a un materiale conduttivo, le correnti vengono indotte nel materiale.
Le correnti indotte fanno uso di sonde array (ECA) per migliorare la versatilità dell’area di ispezione e copertura. Le correnti indotte sono tipicamente utilizzate per: ispezione di scambiatori di calore, superfici di materiali inossidabili, tubi, saldature.
Vantaggi:
- Minima preparazione della superficie da ispezionare;
- In grado di rilevare rotture superficiali e difetti sub-superficiali;
- Non necessita di accoppiante o contatto diretto;
- Può sostituire i metodi superficiali standard;
- Rapidità di esecuzione;
- Registrabile con encoder e dati salvati digitalmente.
Magnetic Flux Leakage (MFL)
Il metodo Magnetic Flux Leakage viene usato per la ricerca di discontinuità in materiali ferromagnetici, utilizzando la saturazione degli stessi. Questa tecnica può essere utilizzata per l’ispezione di tubazioni e linee, l’ispezione del pavimento del serbatoio e altre applicazioni.
Vantaggi:
- utilizzato su tutti i materiali ferromagnetici;
- utilizzato per ispezionare di fasci tubieri con supporti;
- Rapidità di esecuzione.
Remote Field Testing (RFT)
Un campo magnetico viene creato da una bobina e viene ricevuto da una seconda bobina dopo aver viaggiato attraverso il materiale. Questa tecnica consente di rilevare difetti interni ed esterni, anche se non è possibile distinguerli.
Vantaggi:
- utilizzato su tutti i materiali ferromagnetici;
- ricerca di discontinuità interne ed esterne;
- rilevamento di diminuzione di spessore.
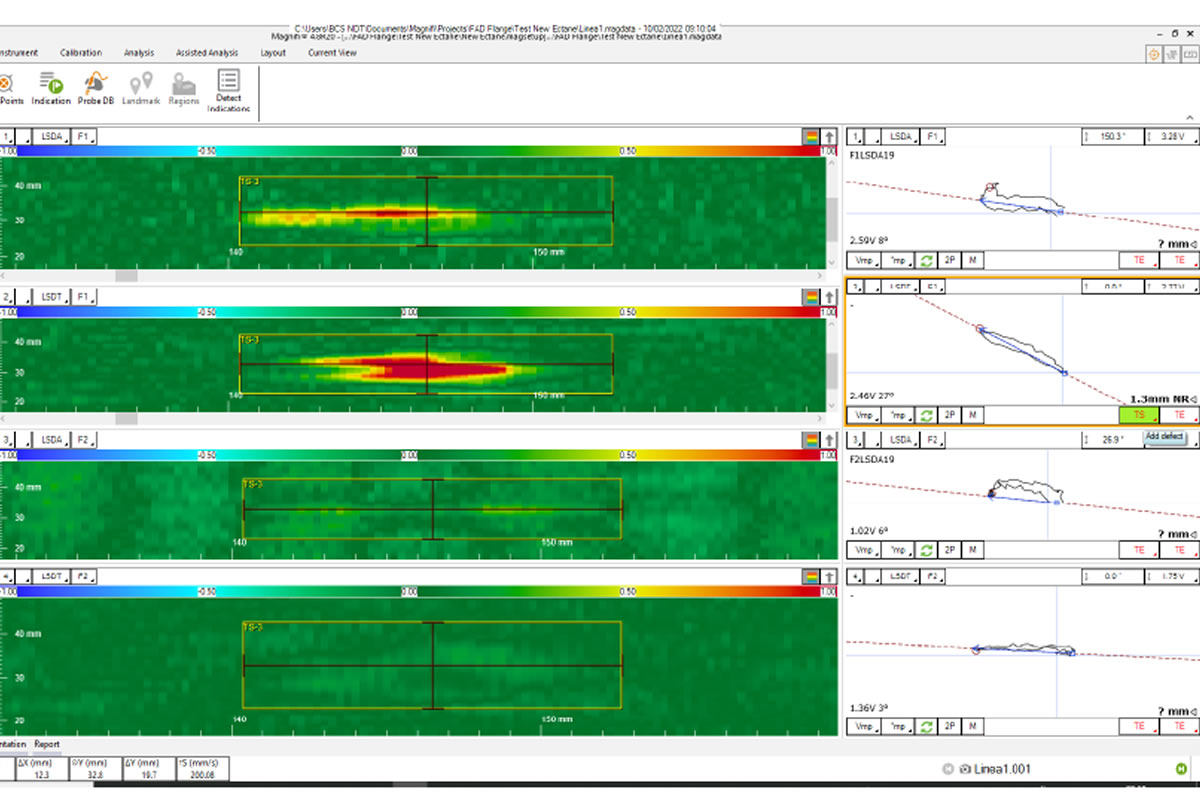
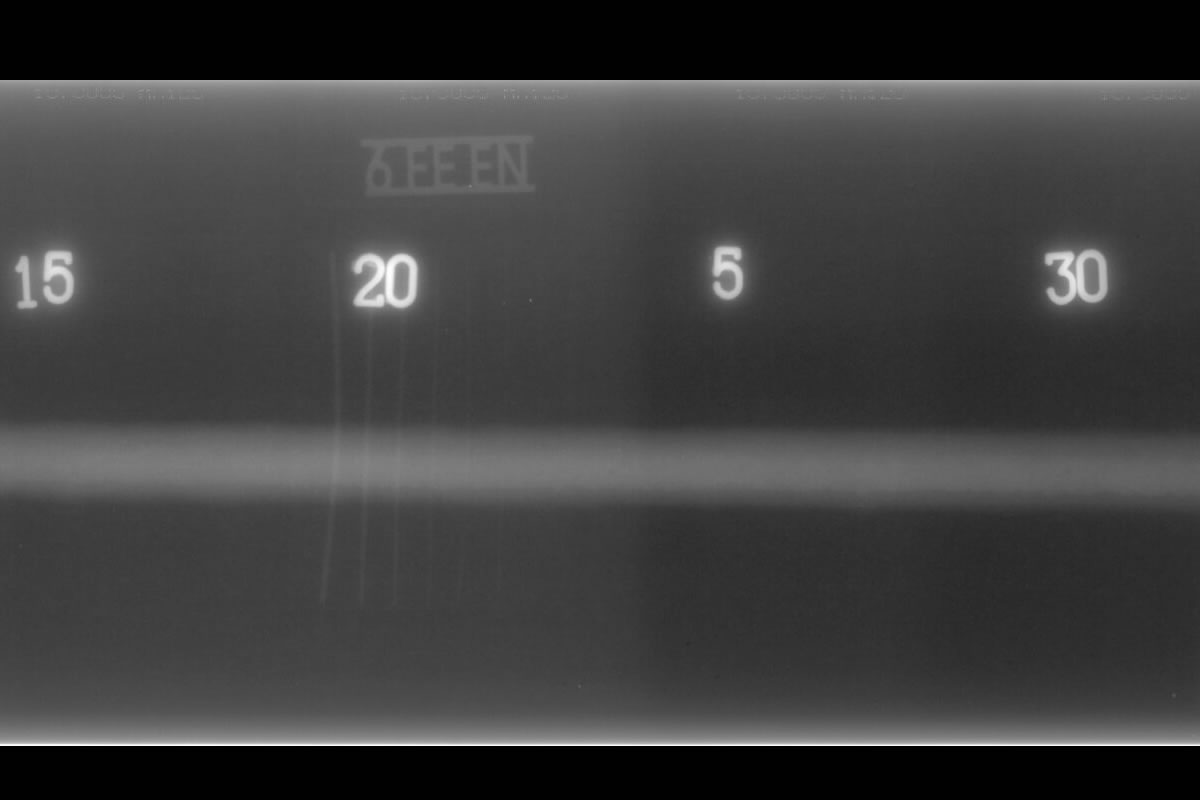
Ispezioni Radiografiche (RT)
La radiografia industriale comporta l’esposizione di un oggetto di prova a radiazioni penetranti in modo che la radiazione passi attraverso l’oggetto da ispezionare e venga resgistrata su un supporto posizionato nel lato opposto dell’oggetto.
I raggi x sono generalmente utilizzati per materiali meno densi (cioè alluminio) o per piccoli spessori di parete. Per materiali più spessi o materiali più densi, vengono utilizzati raggi gamma.
Il supporto di registrazione può essere una pellicola a raggi x industriale o un rilevatore di radiazioni digitale. La radiazione che passa attraverso l’oggetto controllato espone il supporto, causando un effetto finale di aree più scure in cui più radiazioni sono passate attraverso la parte e aree più chiare in cui meno radiazioni sono penetrate. Se c’è un vuoto o un difetto nella parte, passeranno più radiazioni, causando un’immagine più scura sulla pellicola o sul rilevatore.
Le pellicole sono utilizzate nella radiografia su film convenzionali, mentre rilevatori digitali sono utilizzati nella radiografia computerizzata e digitale.
Controllo con Particelle Magnetiche (MPI)
Il test con particelle magnetiche viene applicato per rilevare discontinuità superficiali o vicine alla superficie in materiali ferromagnetici. La sensibilità è maggiore per le discontinuità superficiali e diminuisce rapidamente con la profondità. I difetti tipici che possono essere rilevati con MPI sono cricche, mancanza di fusioni, laminazioni.
Il campo magnetico può essere generato con magneti permanenti (Corrente Continua, DC), che penetra più in profondità nella parte, o elettromagneti (Corrente Alternata, AC).
Le polveri magnetiche secche o umide possono essere utilizzate per il test delle particelle magnetiche e possono essere colorate con un colorante visibile (metodo di contrasto del colore) o un colorante fluorescente (metodo fluorescente).
Le tecniche di magnetizzazione sono generalmente una delle seguenti: puntali, magnetizzazione longitudinale, magnetizzazione circolare, gioghi, magnetizzazione multidirezionale.
I limiti dell’intervallo di temperatura sono dettati dal produttore.
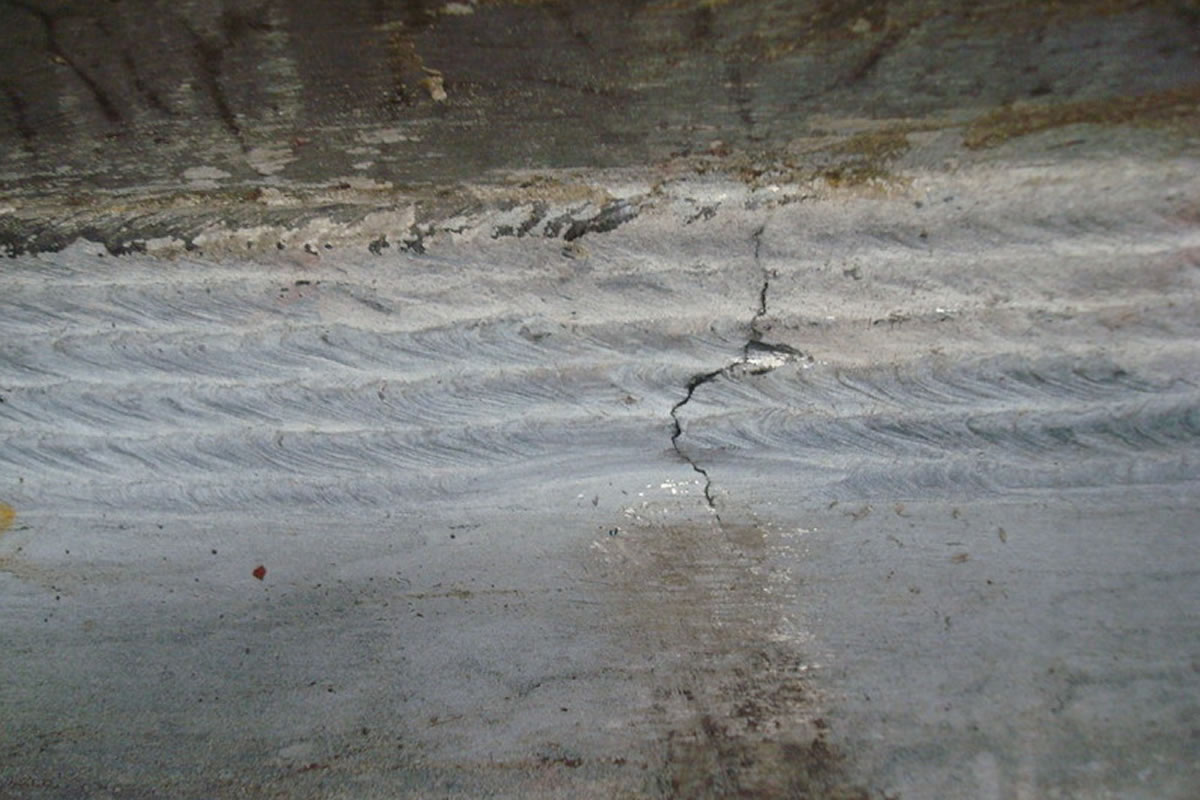
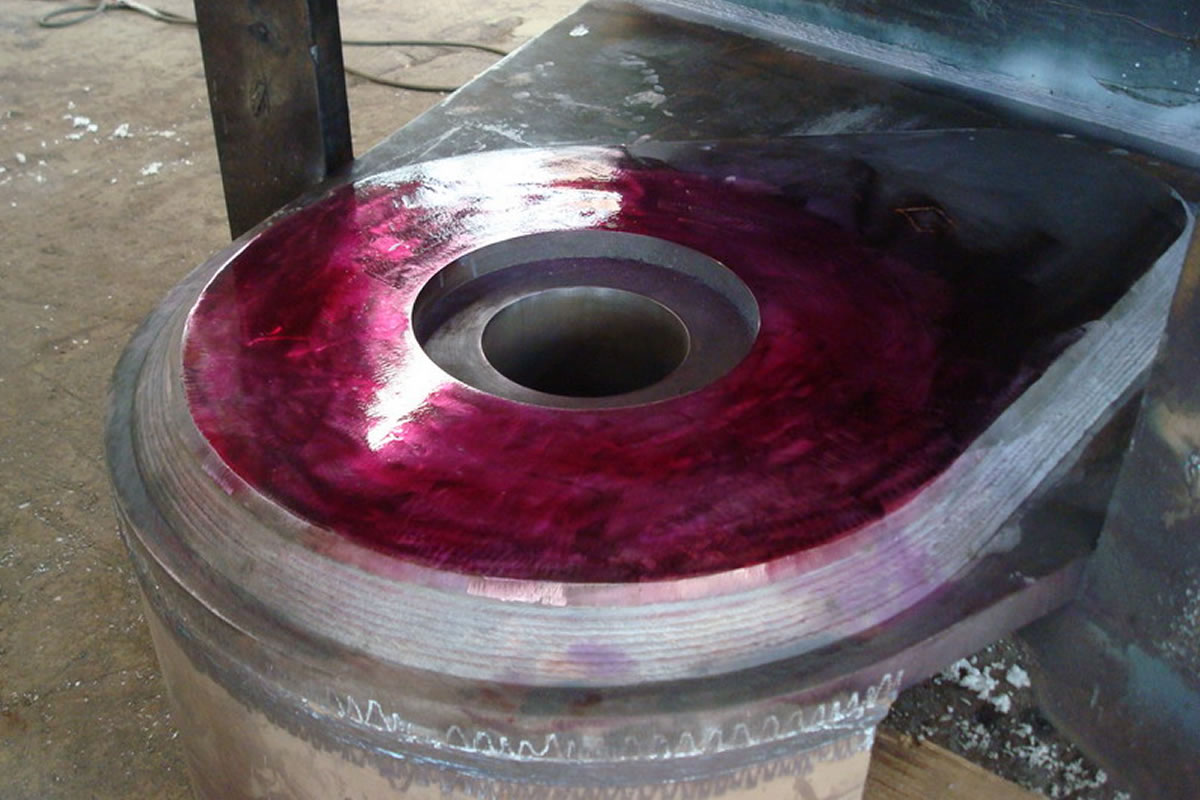
Controlli con Liquidi Penetranti (PT)
Il controllo con Liquidi Penetranti è un metodo utilizzato per rilevare discontinuità aperte alla superficie di materiali non porosi. I difetti tipici rilevati con PT sono cricche, mancanze di fusioni, laminazioni e porosità.
I coloranti possono essere visibili sotto luce bianca (contrasto di colore) o visibili sotto luce ultravioletta (fluorescente). Ognuno di essi può essere utilizzato con una delle seguenti tecniche: lavabile in acqua, post-emulsionante, rimovibile con solvente.
La tecnica standard viene applicata normalmente tra 5°C e 52°C di temperatura. Il metodo può essere utilizzato con temperature al di fuori di questo intervallo, ma la procedura deve essere qualificata in base al codice di riferimento specifico.
Controlli Visivi (VT)
L’esame visivo viene generalmente utilizzato per determinare le condizioni superficiali del pezzo controllato, la forma o le dimensioni delle parti, i disallineamenti, la corrosione o la prova di perdite. L’esame visivo è legato alla maggior parte degli altri metodi, poiché un’ispezione visiva viene spesso effettuata prima o come parte di un altro controllo non distruttivo.
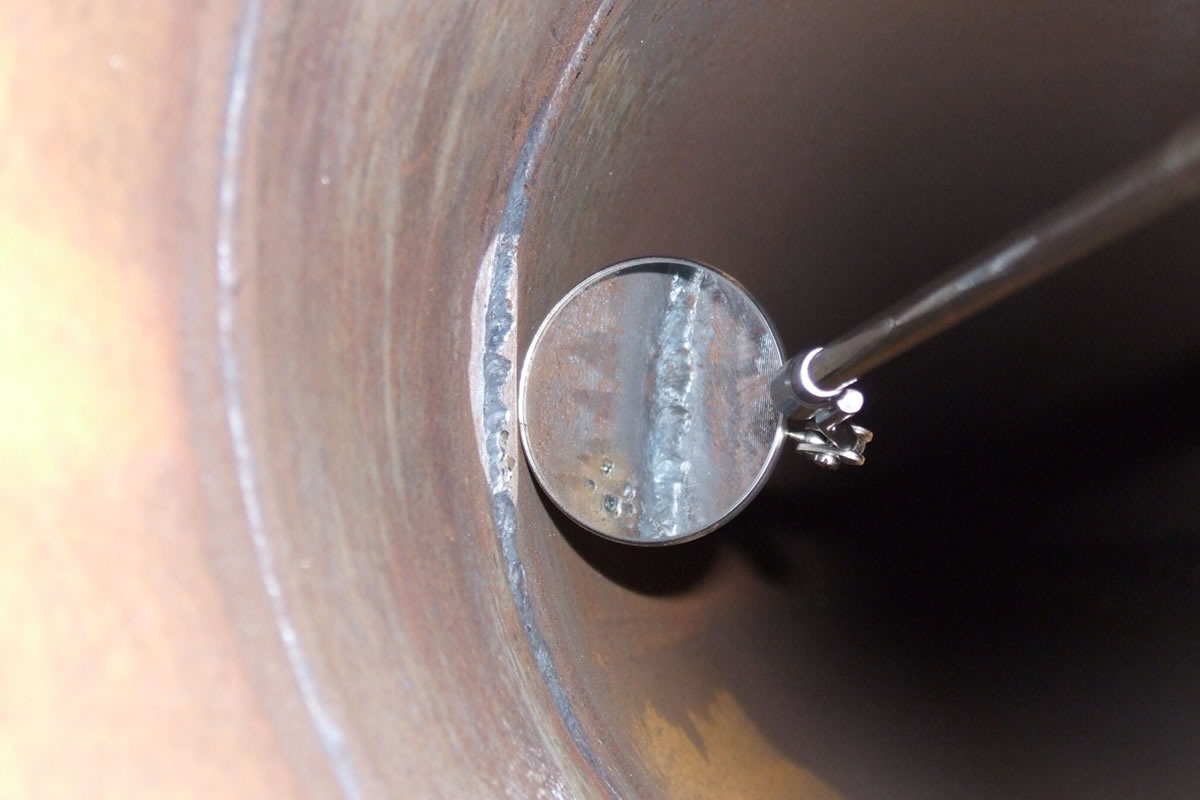
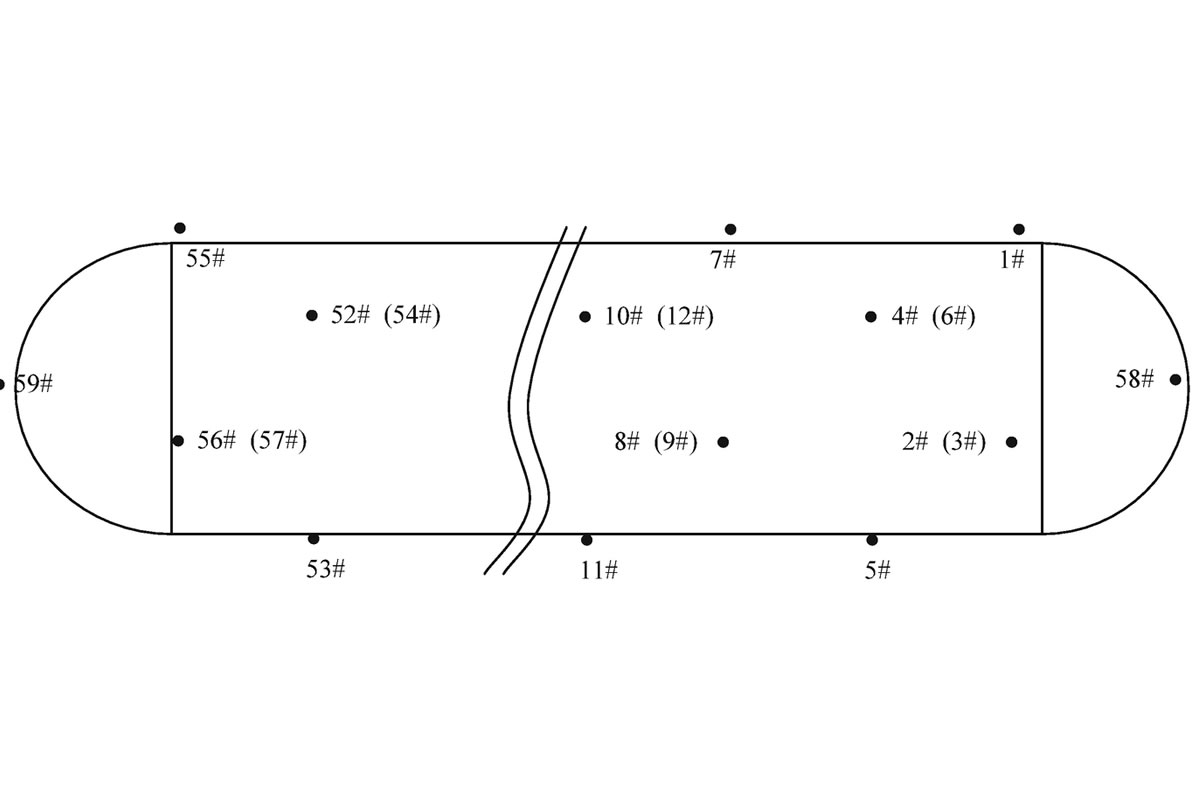
Emissioni Acustiche (AE)*
Il controllo ad emissioni acustiche viene eseguito applicando sensori sul componente da testare. Questi sensori sono in grado di convertire un segnale meccanico in segnali elettrici, che vengono elaborati da un’unità di acquisizione. Queste onde elastiche vengono catturate quando il componente è sottoposto a una forza esterna, come pressione, carico o temperatura. Utilizzando più sensori, le sorgenti di emissione acustica (discontinuità) possono essere rilevate e localizzate nella parte.
Il metodo è in grado di individuare i danni e differenziarli in base alla risposta del segnale. Tuttavia, un’ulteriore ispezione è generalmente necessaria per una valutazione completa del danno.
Come limitazione, il metodo non è in grado di rilevare difetti che non si muovono o crescono.
*Attività non coperta da accreditamento ACCREDIA